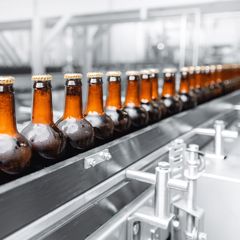
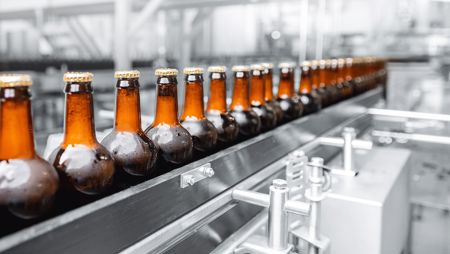
Discover new revenue and reduce expenses
Dynamic connected service capabilities boost uptime, enhance efficiency, and improve resiliency
We help customers delivering exceptional service through for example advanced field service and predictive maintenance. This improves customer satisfaction and decreases operations costs.
While the factory of the future will rely heavily on physical technology like robotics, the software connecting the technology will play just as crucial a role. HSO can help you develop and implement a digital transformation plan to propel your operations into the future. As a top Microsoft partner, we can help you address all aspects of your operation, including ERP, supply chain management, smart maintenance, cloud application development and more.
Critical to digital transformation in manufacturing is getting value out of the vast amounts of data that are available. The challenge is how to capture data, rationalize it and then being able to act on that information. That is where the Microsoft platform and HSO empower companies, creating better results.
A fricitionless experience
Henk-Jan van de Beek, Managing Director HSO CE: “We help our customers with ‘connected scenarios’. This means that we use signals from IoT devices to check if something is wrong and identify the problem. Based on that, a work order can be generated – fully automatically – and an engineer can be scheduled to go and fix the problem.
At the same time, the data that we generate also helps us make better predictions for where preventative maintenance will be needed, avoiding disruptions that affect the user wherever possible.”
“With Dynamics 365 IoT Intelligence, we can rely on meaningful signals and insights, thus reducing the cycle time to action, keeping our teams engaged, and delivering on our promise to our customers.”