How would you rate your organisation's manufacturing agility?
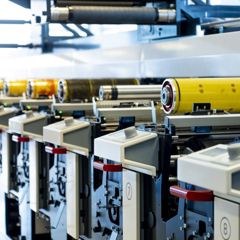
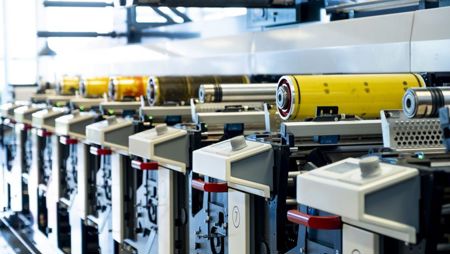
Agility is in the Eye of the Beholder
When the COVID-19 outbreak struck, manufacturing organisations found themselves questioning nearly every aspect of their operations. Manufacturers of all shapes and sizes mobilised to understand the situation, predict what was coming next and adapt the way they operated in response to what was happening. Manufacturers needed to be agile to cope with the constantly changing dynamics; they had little choice.
Virtually overnight, we saw a raft of changes implemented, including the adoption of digital technologies, revised working practices and new supply chains. This was a lesson in agility itself. We even saw numerous firms temporarily repurposing to produce products they probably wouldn’t have made otherwise such as ventilators, face shields and test kits. As a result, a full 90% of UK manufacturing organisations continued to operate through the pandemic, emerging from the other side to produce product another day.
It’s perhaps no surprise, then, that when we conducted this Agility Assessment in 2021, almost three-quarters (74%) of manufacturers felt they were “extremely” or “highly agile”. However, fast forward to today and that sentiment has waned. Indeed, this year’s Agility Assessment reveals that just 47% of manufacturing organisations now believe they are “extremely” or “highly agile” – a drop of 27%.
But why? Speaking to senior manufacturing decision-makers, it became clear that many manufacturers simply overestimated their own agility last year. Having implemented a number of changes to rapidly respond to the unfolding situation, many organisations were left with an artificially inflated perception of their agility. Once the dust had begun to settle and there was scope to take stock – particularly by looking at other manufacturers around them - the true level of their agility became apparent
How would you rate your organisation's manufacturing agility?
10%
42%
37%
10%
As one senior executive, we spoke with said: “If I’m honest, the reason why so many organisations said they were ‘highly’ or ‘extremely’ agile last year is because they genuinely believed they were. “Many implemented programmes to counteract the COVID-related chaos and they survived. “But in reality, most, including us, thought they were better than they were and, as it happens, we were no more agile than anybody else”.
Exacerbating the situation has been the other consequential world events we’ve witnessed over the past 18 months. While many manufacturers did indeed make significant changes to combat the fallout from COVID, few could predict what was to follow.
“Coming out of COVID, most businesses assumed they would bounce back or remain highly agile. However, due to the war in Ukraine, the UK’s political status, the energy crisis and the ongoing Brexit-related supply chain issues, it’s understandable that the perception of agility has dropped”, another senior manufacturing decision maker told us. This was a view frustratingly echoed by a board member at a global automotive manufacturer. “The effort we’re putting into being agile and the work we’re doing has gone up, but our effectiveness has gone down, mainly due to supply chain constraints, particularly chips”, he said.
“The knock-on effect of this is that from an external perspective, we are perceived as being less agile because showroom stock is low and we can’t fulfil what people are asking for. But the truth is we are working hard to even just stay at that level”, he added.
We weren’t as agile as we thought and this has been highlighted by everything that’s happened since the pandemic
Another reason given for manufacturers overestimating their own agility was because of the unprecedented nature of the pandemic. Not only were there rafts of support available, in the form of furlough and government loans, but also customers were far more understanding about longer lead times. As one food and beverage manufacturer told us: “In 25 years, I’ve never known our customers to be so tolerant as they were during the COVID period. It just became accepted that delays with products were inevitable and that seemed to be okay.
“If our customers hadn’t been so understanding, it would have likely caused us to question our agility more”. A similar story was portrayed by the Operations Director at a large plastics manufacturer. “Perhaps many felt it was relatively easy, coping with COVID. After all, most of the rules went out of the window and that left us feeling as though we were in a good position. However, we weren’t as agile as we thought and this has been highlighted by everything that’s happened since the pandemic”, he said.